Creation of a WHS Plan
✅ Paper Type: Free Essay | ✅ Subject: Business |
✅ Wordcount: 2930 words | ✅ Published: 13 Sep 2017 |
Part 1 WHS Plan
1.0 PURPOSE
The purpose of the essay is to prepare a WHS plan which meets the regulatory requirements outlined in S309 WHS Regulation 2011 (NSW). With the help of relevant literature, the essay highlights the WHS plan is an important component in any strategy to make self-regulation work in the construction industry.
2.0 BACKGROUND
The construction industry is recognized as both socially and economically vital and is ruminated to be the most hazardous (Konkolewsky, 2004, Hamalainen et al., 2007). OHS issues in the Australian construction industry are fragmented in nature (Ringen et al., 1995), resulting in continual varying work assignments and worksites (Lingard and Rowlinson 2005). Multiple trades work simultaneously on one site and a different contractor is engaged by each trade (Ringen et al. 1995). The fatality rate is three times the national workplace average (Wild 2005; Cole 2002), about 30-40% of the world’s work-related fatal injuries (ILO, 2010).
3.0 INTRODUCTION
Safety planning is an important and integral part of the construction work process (Hinze, 2000, Carter and Smith, 2006). The S309 WHS Regulation 2011 (NSW) requires the Principal Contractor (PC) for a construction project to prepare a written WHS Plan before work on the project commences. This legislation has resulted in dramatic increase in safety planning and management efforts in the construction industry (Hill, 2004).
In essence, the WHS Plan should outline the PC’s a) WHS roles and responsibilities, b) methods of consultation, co-operation and co-ordination, c) provision of induction and training, d) risk management process, e) subcontractor’s management, f) response to emergency and incidents, g) health and safety rules that are particular to the site and h) steps taken in the direction of assessing, collecting, monitoring, and reviewing safe work methods statements (Johnstone, 1999).
The PC must ensure a copy of the plan must at all times, be readily accessible to anyone carrying out work on the project and is kept until the project is completed (WHS Regulation, 2011).
4.0 ROLES AND RESPONSIBILITIES
To avoid injury and minimise costs, safety planning and integration of OHS deliberations into the various stages of the construction process is essential (Safe Site, 1999, Saurin et al., 2004). All stakeholders associated with a construction project should be held responsible for OHS (Hislop, 1999, Durham et al., 2002). It is also critical to assign OHS responsibilities in the planning stage of a project (RIngen et al., 1995)
Specific WHS responsibilities might include; consultation arrangements (Durham et al., 2002), dissemination of OHS information (HSE, 2005), managing OHS design issues (Smallwood, 1996, Behm, 2005), risk management (Kirchsteiger, 2005, Ringen et al., 1995), managing subcontractors and their compliance with OHS requirements (Mayhew and Quinlan, 1997), conducting OHS induction and other training (Bluff, 2003), inspections (Kartam et al., 2000), incident reporting and investigation (Laukkanen, 1999), developing and implementing emergency procedures (Holt, 2001) and WHS audits (Teo and Ling, 2006) .
5.0 CONSULATION, COOPERATION AND COORDINATION
Worker participation in OHS is an important principle contained in Australian OHS legislation (Ayers and Culvenor, 2002). Arrangements for consultation must be put on place such as pre-start briefings (HSE, 2005), toolbox talks (Trethewy et al., 2003), conceptual and preliminary design phases (Szymberski, 1997), risk assessment process (Trethewy et al., 2000), implementation of employee-elected health and safety representatives (Durham et al. 2002), role of unions (Cole, 2003) and a system for communicating site-specific WHS rules (Toole, 2002). Lin and Mills (2001) and Nishgaki (1994) advocated that safety committee with representatives from the employer, worker and subcontractor promotes interaction, improve trust and communication, prevent incident and enhance safe work habits.
6.0 INDUCTION AND TRAINING
To improve OHS, training in the construction is paramount (Davis and Tomsasin, 1999). Under Section 317 of WHS Regulation 2011, the PC must ensure that general construction induction and site specific induction training is completed by all workers before any site work is executed (Kartam et al., 2000). Training will also be required in the following situations: when new WHS hazards or risks arise as a result of new tasks, systems, plant and equipment (Arboleda and Abraham, 2004), introduction of substances (Nishgaki et al., 1994), changes to workplace (Lin and Mills, 2001), incident prevention (Laukkanen, 1999), provision of written safe work procedures (Gun and Ryan, 1994), and changes in the regulatory requirements (Teo et al., 2005). The inclusion of emergency and first-aid training (McKenna & Hale, 1982) will increase realistic worker perceptions about occurrence of accidents (Lingard, 2013). Refresher training should be provided at regular intervals(Trethewy and Gardner, 2000).
7.0 RISK MANAGEMENT
OHS management is underpinned by the concept of risk (Kirchsteiger, 2005). Ringen et al. (1995) supported an integrated approach to risk management where responsibility is shared amongst the stakeholders. All stakeholders shall be working collaboratively to identify hazards, assess and mitigate risks for the project (Matthews, 1993, Kirchsteiger, 2005). Site-specific project risks register shall be developed incorporating all high-risk construction work activities on the project (Holmes et al., 1999). In the design stage of construction, Campion (2000) deliberated that the following be considered: a) site remediation and methods (asbestos, lead), b) excavation c) adequate ground conditions and type of control medium (shoring, trench boxes), d) silica content and machinery types to mitigate dust and e) making sure a stable structure exists during deconstruction or reconstruction.
8.0 EMERGENCY AND INCIDENTS RESPONSE
Emergency planning is a significant part of incident management. An evacuation procedure comprising information about emergency contacts and services, medical treatment and assistance, communication of emergency instructions to relevant workers at the site, regular emergency drills, showing location of emergency exits, fire protection equipment and assembly areas shall be provided (Lingard and Rowlinson, 2005). Routine site inspections shall ensure the means of access and egress are unobstructed and operable (Hallowell and Gambatese, 2009).
Arrangements for the reporting, investigating, and corrective actions in response to incidents and injuries (Lingard and Rowlinson, 2005), notification to the regulator if the incident is a ‘notifiable incident’ (WHS Regulation, 2011) and the requirements for the investigation of incidents shall be established (Henderson et al., 2001). Incidents shall be reported to the supervisor first and then to PC. Marks et al. (2014) emphasised the need for near miss reporting as a positive experience to capture the benefits throughout the construction project and enhance OHS performance.
9.0 MANAGING SUBCONTRACTORS
Procedure for engaging, monitoring and reviewing of subcontractors shall be effected (Mayhew et al. 1997). Periodic evaluation of subcontractor’s OHS performance shall be carried out by PC using inspections and audits to ensure they are working safely (Kartam et al., 2000, ILO, 1992).
There shall be arrangements for collection, monitoring and reviewing of all subcontractors risk assessments, SWMS and their OHS performance (Borys, 2012). A register containing information on insurances, licenses, accreditation information and verification of documents of all the service providers shall be implemented (SafeWork Australia, 2010).
10.0 SITE SAFETY RULES
Johnstone (1999) pointed out that PC must communicate their expectations of site safety rules throughout the project’s duration to all workers through site specific induction (Kartam et al., 2000). Site safety rules should be practical in nature, reflect the influential abilities of each construction party and shall be project and company specific (Toole, 2002). Hale and Borys (2010) proposed a “rules for rules” approach to safety rules that would make provisions for handling exceptions and endorse discretion to modify and adapt the rules under certain conditions. Such an approach gives more credence to the social construction of safety under conventional approaches to writing safety rules. This approach will ultimately determine the type and number of rules needed.
Campion (2000) articulated provision of amenities/services and site security/access, traffic management. Ringen et al., (1995) emphasised that eating and sanitary facilities as well as use of personal protective equipment (PPE) provided for construction workers will reduce exposure to hazards and maintain OHS standards.
The PC shall also manage construction hazards such as fall from heights and falling objects (Trethewy et al., 2003), demolition work, excavation work/trenching, scaffolds, ladder safety (Helander (1991), work near overhead or underground essential services, electrical (Durham , 2002), plant (HSE, 1985), noise (Blackmon and Gramopadhye, 1995), manual handling (Straker et al., 2004), slips, trips and falls (Bentley & Haslam, 2001), sun safety (Madgwick et al. 2011), hand operated and power tool use (Lingard and Rowlinson, 2005).
11.0 SAFE WORK METHOD STATEMENTS (SWMS)
The National Standard for Construction Work (NOHSC:1016 (2005)) stipulated that ”each person with control of over high-risk construction work including sub-contractors and self-employed persons, gives the person with control of the construction project a written safe work method statement (SWMS) for the high-risk construction work to be carried out, before commencing that work. According to the standard, high-risk construction work means any one of 19 activities shown in Table 1.
The Office of the Federal Safety Commissioner defined SWMS as a document that identiï¬es hazards, assesses the risk of those hazards occurring and determines the risk controls that must be established (OFSC, 2010). The SWMS is essentially a ”process rule” for PC and an ”action rule” for the workers (Borys, 2012). All reasonable steps shall be taken by the PC to attain a SWMS from contractor carrying out high risk construction work before the work commences (SafeWork Australia, 2010).
The SWMS shall reflect the specific circumstances and work environment of the workplace where the high risk construction work is to be undertaken and consulting with the workers carrying out the work (Rozenfeld et al. 2010). The PC shall ensure that SWMS are followed by all workers (including contractors and subcontractors) using regular site safety inspections and audits (ILO, 1992). If the SWMS is not complied, that work is terminated and the SWMS is reviewed and as necessary revised (NOHSC, 2005).
Workers are required to be licensed to undertake high risk work such as rigging, dogging, crane, earth moving machinery and forklift operation (SafeWork Australia, 2010).
Part 2 Codes of Practice and Standards
Part 3 Compare and contrast factors which contribute to effectivemanagement of OHS in construction and manufacturing industry.
1.0 PURPOSE
With the help of relevant literature, the essay highlights factors that contribute to effective management of OHS in construction and manufacturing industry.
2.0 INTRODUCTION AND BACKGROUND
OHS in construction involves unique challenges (Hallowell and Gambatese, 2009) and construction firms shall provide a safe working environment for their workers (Lin & Mills, 2001). The manufacturing sector faced global competition, created an environment of new management practices and has influenced ways of managing OHS (MacIntosh & Gough, 1998). Basu and Wright (1997) considered OHS management to be one key element of a successful manufacturing organization.
3.0 KEY FACTORS WHICH CONTRIBUTE TO EFFECTIVE MANAGEMENT OF OHS IN CONSTRUCTION
Firm size
McVittie et al. (1997) and Wilson (2000) illustrated that large firms tend to deal with OHS more effectively. Numerous factors contributing to this phenomenon included experience, resourcing, training and policy development (Lin & Mills, 2001). It is also plausible that formal documentation procedures mandated by OHS legislation do not fit the traditions and needs of small and medium companies (Hale and Baram, 1998).
Management leadership
Sawacha et al. (1999) emphasised management’s support, participation and commitment are linked to OHS performance. Hinze (1988) and Jaselskis (1996) observed that regular and active involvement by the management play a significant role in determining the OHS performance.
OHS in Design
Decisions made in the design stages of construction projects can have major OHS implications (Behm, 2005, Coleman, 1991). Cole (2001) highlighted that OHS shall be considered in all aspects of the design process. Jeffrey and Douglas (1994) reviewed the OHS performance of the construction industry and identified a robust relationship between design decision and safe construction.
Training
Hale (1984) indicated that training of workers can lead to improved OHS on construction site.Petrovic-Lazarevic (2007) and Davies and Tomasin (1999) advocated training to nurture safe work practices and change workers’ attitudes towards safety in construction industry.
Workforce characteristics
“Casualised” workers dominate the construction workforce (Hislop, 1999) and have been associated with poor OHS performance due to high labour turnover (Kartam et al., 2000). Owing to aging population with a dearth of experienced, qualified construction workers (Hislop, 1999), the young labour force absence of “skills and experience” was unable to manage OHS risk appropriately (Barr, 2006).
Employee attitude and organisational culture
Andriesson (1978) and Zohar & Luria (2003) noted that supervisor coaching and feedback, respecting their workers contribution can have a positive impact on workers’ OHS performance. OHS performance can be attributed by exemplary culture and conducive workplace conditions (Prasad and Reghunath, 2010).
Consultation and Communication
Sawacha et al. (1999) and Nishgaki (1994) revealed that safety committees positively contribute to OHS performance. Mechanism such as pre-construction site reviews gives an opportunity for workers to be consulted and address OHS concerns (Harper, 1998). Hopkins (2005) described mindful leadership where frequent visits to worksites and actively engage with and listen to what workers have to say about OHS.
Literacy
About 7% of the working population are employed in the Australia construction industry and Non-English Speaking Background (NESB) accounted for almost 12.5%. (ABS, 2004). Low english proficiency amongst NESB workers is a contributory factor in OHS communication. OHS training should be provided in a range of languages (Trajkovski & Loosemore, 2006).
Hazard and risk assessment
Holmes (1999) alluded that OHS risk should be identified prior to construction and will lead to a much higher OHS standard. Kirchsteiger (2005) claimed that clear hazard identification, risk assessment and mitigation actions are fundamental for effective OHS risk management and performance.
Inspections and Audits
Nishgaki (1994) and Hinze (1988) recommended that regular site inspection by management advance OHS performance. Cameron and Duff (2000) developed a “management and operative safety behaviour audit” for the construction industry designed to measure OHS performance.
4.0 KEY FACTORS WHICH CONTRIBUTE TO EFFECTIVE MANAGEMENT OF OHS IN MANUFACTURING
Firm size
Leigh (1989) and Vredenburgh (2002) discovered proactive OHS management practices are represented in large manufacturing firms. Lamm & Walters (2004) established that SMEs faced challenges in their capacity to manage OHS due to their limited resources and expertise. Bluff (2010) showed that large manufacturing firms performed better in OHS outcomes for hazard recognition, risk control and plant safety information.
Management leadership
Cox and Flin (1998) and Park and Butler (2000) stated that active role and commitment of management influence workers’ safety and OHS performance. According to Wright (1996), management accountability and ownership of OHS is considered a necessary precursor for improving OHS management.
OHS in Design
Kletz (1998) emphasised the prominence of addressing OHS from design stage to eliminate hazards. Bluff (2010) established that manufacturing firms perform well across chains of OHS outcomes such as comprehensive hazard recognition, using safe and innovative controls when user input at the design stage are sought.
Training
Zohar (1980) established that training about OHS practices shall be implemented in manufacturing companies resulting in workers becoming more productive and safer work environment (Vassie and Lucas, 2001) will eventuate. In manufacturing sector, workplace-based informal OHS training will suit mature-age workers (Callan, 2007).
Workforce characteristics
The manufacturing industry has high number of mature-age workers due to aging workforce.
Changes in apprenticeship system cause a reduction in skilled workers compounded by an increase in overseas workers with different safety knowledge and language barriers (ABF, 2011).
Employee attitude and organisational culture
Griffin and Neal (2000) identified OHS management as a key factor underpinning the safety climate in a manufacturing organisation. Breslin et al. (2007) addressed that young male workers are passive in communicating about OHS matters compared to young female workers who are more concerned about OHS.
Consultation and Communication
Vassie and Lucas (2001) discovered that by empowering employees to take active roles in managing OHS, higher OHS performance was achieved. Team coordination and cooperation is known to have a strong effect on OHS (Mathieu et al., 2008).
Literacy
In Australia, manufacturing sector employs 8.7% of the population and has high number of mature-age workers with low literacy and qualification levels (ABF, 2011). For these workers with cultural and linguistically diverse background, OHS communication was a barrier (SafeWork Australia, 2013).
Hazard and risk assessment
Vassie and Lucas (2001) and Gadd et al. (2003) commended that risk assessment was conducted by interdisciplinary team to take into account different interests, perceptions and assumptions about risk. Karageorgiou et al. (2000) inferred that risk assessment may be a key method in contributing to effective OHS management.
Inspections and Audits
Bunn et al. (2001) established that audit in manufacturing organisations are a proactive measure to improve OHS outcomes and helps to develop strategies for OHS success. Specific areas for OHS improvement and ways to prioritise actions based on audit were identified (Perkinson, 1997).
5.0 SIMILARITIES AND DIFFERENCES BETWEEN THE CONSTRUCTION AND MANUFACTURING INDUSTRY
Firm size
The firm size of both construction and manufacturing industry has a positive impact on OHS management. Large enterprises do well as they are more resourced and experience to manage OHS effectively (Lin & Mills, 2001, Leigh, 1989).
Management leadership
Both construction and manufacturing industry identified that active role and management commitment improved OHS management (Wright, 1996, Sawacha et al., 1999).
OHS in Design
Addressing OHS at the design stage in construction and manufacturing produced better OHS outcomes (Behm, 2005, Kletz, 1998).
Training
Training provided for workers generally lead to improved OHS, resulting in workers becoming more productive and safer work environment will eventuate (Hale, 1984, Zohar, 1980).
Workforce characteristics
Construction workforce is “casualised” whilst manufacturing workforce are of mature-age (Hislop, 1999, ABF, 2011). Due to aging population, young labour force absence of “skills and experience” is unable to manage OHS risk appropriately (Barr, 2006).
Employee attitude and organisational culture
Supervisor who respects their workers and their contribution enhanced OHS performance. Conducive working conditions contribute to OHS (Griffin & Neal, 2005, Zohar & Luria, 2003).
Consultation and Communication
Safety committees in construction play a positive role in the improvement of OHS performance whilst empowering workers in the manufacturing sector to take active roles in managing OHS was the key (Nishgaki, 1994, Vassie & Lucas, 2001).
Literacy
Workers in the construction and manufacturing industry have low english proficiency and is a causation factor in safety communication (ABS, 2004, ABF, 2011). Both industries identified the need for OHS to be provided in languages other than English (Trajkovski & Loosemore, 2006).
Hazard and risk assessment
OHS risk should be identified prior to construction whilst in manufacturing, an interdisciplinary approach to risk assessment is the key to effective OHS management (Holmes, 1999, Vassie & Lucas, 2001).
Inspections and Audits
In construction and manufacturing, regular site inspections by management advance good OHS outcomes. Audits help to develop strategies for OHS success (Hinze, 1988, Bunn et al., 2001).
6.0 CONCLUSION
Based on the findings, similarities exist in key factors contributing to effective management of OHS in construction and manufacturing industry with the exception of hazard and risk assessment, workforce characteristics and audits. The differences are in approach and methodology, but they still have an important role in OHS performance.
REFERENCES
Cite This Work
To export a reference to this article please select a referencing stye below:
Related Services
View allDMCA / Removal Request
If you are the original writer of this essay and no longer wish to have your work published on UKEssays.com then please click the following link to email our support team:
Request essay removalRelated Services
Our academic writing and marking services can help you!
Related Lectures
Study for free with our range of university lecture notes!
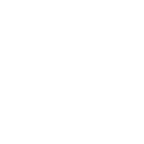
Freelance Writing Jobs
Looking for a flexible role?
Do you have a 2:1 degree or higher?
Study Resources
Free resources to assist you with your university studies!